Pedal Assist Systems
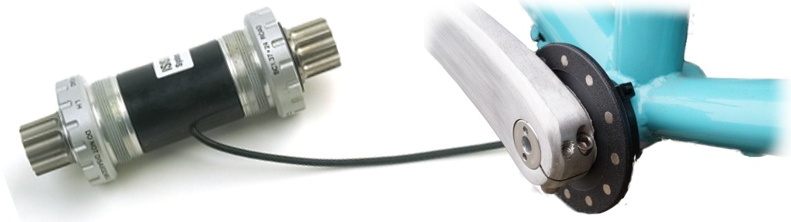
In ebike terminology PAS is an abbreviation for Pedal Assist System, and it's a general term for devices that power the motor automatically when you pedal without the need to press a throttle on the handlebars. They can do this in response to the speed that you are spinning the cranks, the torque that you are applying to the pedals, or some combination of those. Ebikes with this behaviour are often called pedalecs.
Pedal Assist Systems and pedalec ebikes have been around since the early days of electric bicycles, such as the Charger from the 1990s. When we first got into ebikes in the early 2000's we thought that they were a little bit gimmicky. You have a throttle on the handlebar that gives you 100% control of the motor power at any instant, giving you the ability to increase or decrease the assist at will. Why would you want anything different?
Benefits of PAS
The main benefit of PAS on an ebike is that you can get power assist without using the throttle. You wouldn't think that using a throttle is a big issue, but on long trips or even regular commute it can become somewhat tiring to always modulate a throttle for your desired power. Twist throttles can result in an uncomfortable wrist position and thumb throttles mean having your thumb extended. Yeah first world problems. But when you ride a bike under PAS control the motor simply engages automatically and you don't need to do anything with your hands, and it's oddly quite liberating.
A PAS controlled ebike will usually have a control button on the handlebars to set the assist level, so you can still increase or decrease the motor power while riding. Unlike riding under throttle control though, you only interact with the system when you want a change in the amount of assistance rather than all the time. We went from pooh-poohing PAS setups to wholly embracing them once we realized what we were missing, and we developed the V3 Cycle Analyst device in large part as a universal tool to bring PAS functionality to virtually any ebike system.
Why wouldn't you want PAS?
On the other hand, there are some situations where automatic pedal assist is either not appropriate or even dangerous. For instance, if you are riding in a busy city full of stop and go traffic, sudden obstacles to avoid, and lots of nudging along at low speeds, the presence of automatic power whenever you pedal can result in motor bursts when you really don't want them. Users who only want the electric assist for hills and accelerating from a standstill would find a PAS setup unnecessary. And really powerful ebikes that ride more like dirt bikes are also generally better controlled like a dirt bike with handlebar throttle.
Sensor Types
Broadly speaking pedal assist systems fall into two categories, basic PAS sensors which detect just the speed at which the cranks are turning, and torque sensors which also sense how hard the rider is pushing on the pedals.
Basic PAS Sensor
The most common type of basic PAS sensor involves a magnet ring attached to the crank arm or spindle, with a sensor that detects the passing magnets when the pedals are turned. Other sensors are more neatly integrated into a tight package (PAS mini sensor) or are built into the bottom bracket itself for a very clean install. There are also PAS sensors that sense the passing teeth on the chainring or cog.
With a basic PAS sensor, the control electronics only knows how fast you are spinning the cranks, but it does not know how much force you are actually applying. Usually these systems produce a set amount of power whenever you are pedaling, although more sophisticated schemes will also vary the assist in some capacity with the cadence too.
One of the critical variables in a basic PAS sensor is the number of magnetic poles or electrical pulses per wheel revolution. The more PAS poles on the sensor the more immediately the electronics can respond to your pedaling. Early PAS sensors usually had just 5 or 6 magnets on the ring, and you would need to turn the cranks about half a rotation before getting power assist, and there was similarly a noticeable lag from when you stopped pedaling before the power would cut out. These days 12 poles is the norm and we increasingly see PAS sensors with 24 poles and even higher. These higher pole sensors enable a control system to have much faster pedal response.
Torque Sensors
A torque sensor needs to measure the force that the rider is applying to the pedals. Typically these take the form of an entire replacement bottom bracket which has internal force sensing built into it. But other systems measure the force on the chain, the rear dropout, the rear axle, cogs, or pedals. See this later section for a full list of force sensing techniques. To be precise most of these sensors aren't directly measuring torque itself although they all fall under the umbrella name "torque sensor".
The bottom bracket sensors are the most common for aftermarket ebike conversions, as you simply replace the existing BB on the bike. The majority of these sensors come with square taper spindles, although there are a few ISIS options as well. They also generally require that the frame has a standard 68mm wide threaded bottom bracket shell (sorry 73mm folk) with a hole drilled in it for cable exit. The BB sensors also come in a range of spindle lengths and you would normally select one that is a close match to the length of the original BB on the bike in order to maintain the original chainline, though being a few mm longer or shorter is usually of no consequence.
With torque sensing PAS, the motor power is usually dialed in to amplify the rider's pedal effort. This is often expressed as a multiplier on the rider's pedal power, so it could match 1:1, or say double it so that for every watt of human power the motor puts out 2 watts. When you pedal harder you get more power, and if you pedal lightly you get minimal power.
For people who like to feel that they need to 'earn' motor power by pedaling harder, a torque sensor is pretty ideal. It enables the feeling of a Bionic connection between the bike and the legs. Similarly, for riders who are interested in monitoring and recording their own human power output in watts, an ebike torque sensor and V3 Cycle Analyst costs just a fraction of a commercial bicycle power meter.
Which is Better?
This is one of those questions with an "it depends" kind of answer. Many people will assume that a torque sensor is ideal and represents the gold standard for PAS control, and that the basic PAS sensors represent a poor but inexpensive alternative. We don't think it's that simple, as people who prefer to regulate motor power independently from their pedal effort will be better served with a basic PAS setup.
A torque based control directly couples the motor power to the rider's power output. That means that going uphill you need to pedal hard to get sufficient power to climb, while on the flats or downhill’s if you pedal hard you will end up getting motor power when you don't actually need or want it. The overall experience is similar to riding a non electric bike, where your riding efforts vary significantly with the terrain; sweat going up, take it easy going down. If that is the behavior that you want then it works extremely well.
On the other hand, one of the benefits of an ebike is that you can use the motor to decouple the terrain from how hard you need to pedal. The motor can make up the difference between what your legs are putting out and what is required for the given hill and headwind. If you want to be able to ride comfortably with a given effort that doesn't change much whether going up or down, then you'll need the motor to put out lots of power when climbing, and then minimal to no power on the downhills, even while leg power remains the same. A basic PAS sensor with an easily handlebar adjustment for the PAS power level allows you to achieve this behavior quite nicely. It provides independent control of motor power and your pedal effort like a throttle, but without needing to constantly hold a throttle position.
Signal Levels
It's essential to know what kind of signals are output by the sensor in order for it to interface with an ebike system. At the moment, most PAS sensors are based around digital 0-5V pulses for the basic PAS cadence signal, and an analog voltage for the torque signal. However the exact nature of those signals can vary a lot and there is no direct interchangeability between different products.
Signal Types for Basic PAS Sensors
The signal from a basic cadence sensor needs to differentiate between the cranks spinning forwards versus backwards. That's because the pedals will turn backwards whenever you roll the bike in reverse, which happens all the time when pulling it out of a bike rack etc., and if this causes the PAS function to kick in and turn the motor on then you have quite a surprise.
A majority of basic PAS sensors on the market have just one signal line in addition to 5V power and Gnd. This signal pulses up and down as the pedal is rotated forwards, and does nothing if the pedal is rotated backwards. That makes the interface logic very straightforward, but it forces the sensor to only work on one side of the bike. If you install a sensor intended for the right crank on the left side of the bike (say for better mechanical clearance), then it would see you pedaling backwards all the time and do nothing.
There is a variant to this 1-wire sensor that pulses both with forwards and reverse rotation, but the pulse width changes between the two. For instance, forwards rotation might have a long HIGH state, and a short LOW state, while this is inverted when pedaling backwards. The control system must be programmed to discern based on relative pulse width if it is the forwards or reverse pedal direction and only respond accordingly. It also requires the detection of several pulses before it can positively identify forwards or reverse direction, so normally there would be a slightly longer delay before PAS power kicked in.
Finally, most of the PAS sensors offered by Grin use a 2 wire quadrature signal for the cadence sensing, with two signals that toggle up and down out of phase with each other. Pedal direction is then determined by the order sequence of the two pulses. This method is also used in a majority of the bottom bracket sensors. It offers the most versatility for distinguishing forwards and reverse rotation, allowing installation on either side of the bike frame, and allowing backwards pedaling to have a control function (such as activating regen). However, it does require 4 wires in total, 2 signal wires along with Power and Gnd.
Force Signal
The torque signal from these sensors is usually a straightforward voltage in the 0-5V signal range. The table below shows the resting voltage with no torque on the crank and the voltage you get with maximum torque for various sensors that we have offered. Notice how some sensors start at 2.5V and then decrease in voltage as torque is applied, others increase in voltage, and none have the same overall scaling for Nm / volt.
Sensor Type | Offset Voltage | Full Torque Voltage |
THUN / NCTE | 2.5 V | 0.5V |
TDCM | 2.5V | 3.3V |
SEMPU | 1.5V | 4.0V |
Cycle Stoker | 1-2V | 4.5V |
With a V3 Cycle Analyst, you can see all of these signals in real-time in the setup menu. The state of the two basic PAS input wires is shown in the basic PAS preview screen, there is a small arrow beside the 'P' and 'D' signals that will point up when they are at 5V, and down with they are at 0V.
Similarly, on the torque sensor setup menu you can see the actual voltage of the sensor device along with a display on how it is scaled into Nm of torque. By applying a known force on the cranks, you can confirm that the conversion into Newton-meters is in the right ballpark. A 60 kg person is standing with all their weight on a horizontal 165mm crank is producing (60 * 9.8 * 0.165) = 97 Nm of torque. Note that sensors that measure only the left side torque should have their Nm/V scaling doubled from the actual value, and other sensors (like the TDCM) have signals that saturate well before this 100 Nm point, and would need to be calibrated with something lighter than a human body weight on the crank.
Be aware that torque sensors in general have both a torque signal AND a cadence signal. That is essential to know how much power the rider is putting out (which is torque*rpm), as well as for safety. If the ebike could be powered from the torque signal alone even in the absense of any pedal rotation then setup errors or drifts in the signal level could cause the bike to take off even with no throttling or pedaling from the rider.
Sensor Power
In addition to the signal wires, the sensor also requires a power and Gnd wire. Most of the basic PAS sensors are designed to run off of 5V, while many torque sensors require higher voltages to operate, like 10-16V for the THUN, or 10-60V for the Sempu. On the V3 Cycle Analyst, we chose to use a 10V power bus on the 5-pin PAS plug for compatibility with these torque sensors. We then had our supply of basic PAS sensors all modified with an internal regulator so they would function at 10V as well. If you want to use the CA3 with a basic PAS sensor, or a torque sensor that is only meant to be powered from 5V, you need to either add a 5V regulator to the line or swap the 10V wire with a 5V wire from the throttle or Aux plugs. Otherwise you may damage the sensor and potentially the CA3 as well.
Methods of Torque Sensing
There are many methods for sensing the force that a rider is putting into the system. These are typically lumped all in the same name of 'torque sensors', but strictly speaking most of these aren't actually measuring torque directly.
-
Spindle Torque
In these sensors, the torque is measured across the bottom bracket spindle. The torque can be sensed with strain gauges and a slipring to couple power to the spinning sensor, it can be measured optically by the alignment of disks on either side of the spindle, or it can be measured with magnetostrictive technology, such as the early to market THUN torque sensors. The downside with measuring spindle torque is that it only senses the force that the rider applies with the left pedal crank, as the right pedal effort goes directly to the chainring without passing through the spindle. As a result, some extra care is required in the electronics to compensate for the lack of a right side pedal signal. -
Chainring Torque
The most accurate location to sense human power is on the front chainring mount itself, since this has the combined net torque from both the left and right pedals before any mechanical losses and is a direct measure of the mechanical torque into the system. The challenge is that this is a rotating reference frame and so a wireless coupling is required. Certain ebike torque sensors like the ERider and Sempu TMM4 products operate this way and have a separate mount for the chainring spider that is independent of the right crank, with a wireless bridge inside the bottom bracket housing to couple power to the rotating spindle. Most commercial power meters used by competitive cyclists operate on a similar principle but tend to use a battery on the crank for powering the force sensing circuitry with a wireless data link to a display. . -
Chain Tension
Another fairly direct way to measure the rider input is by sensing the tension in the bicycle chain itself. The BeamTS from Santa Monica EV and the Cycle Stoker are both example of torque measurement using idler pulleys to sense the chain tension. It's also possible to deduce the chain tension without an idler from a measure of the chain's resonant frequency, though we haven't seen any products based on this. Chain tension in and of itself is not the same thing as torque, as a given torque will produce more and more tension the smaller the front chainring. So a derivation of human watts from chain tension and pedal cadence requires awareness of the front chainring size, not really an issue for providing proportional assistance but it does matter for computing accurate human power in watts. -
Rear Dropout Sensor
The tension in the chain results in a forwards force on the right side rear dropout, and this provides another means for sensing the rider's pedal effort. The TMM4 is an ebike torque sensor designed around this principle. It is a stand alone dropout with an integrated force sensor to measure the forwards pull of the chain. This is an inexpensive solution since it can benefit from using very simple force sensing technology on a static part of the frame, and is quite popular on OEM ebikes (such as Stromer and Juiced) that can customize their frame to fit the sensor. This required frame customization to accommodate their dropout puts it largely out of the realm of DIY ebike builds though. -
BB Reaction Force
Just like there is a forwards pull from chain tension on the right side rear dropout, there is also a backwards pull on the right side of the bottom bracket. The TDCM bottom bracket sensor exploits this principle. The right side crank spindle bearing is supported in a slotted rather than a round cavity, and when the rider pedals hard the chain tension pulls the spindle backwards slightly in this slot. An inexpensive magnet and hall sensor is used to sense this flex backwards. -
Rear Axle Flex
The chain tension pulling on the cog not only pulls the rear dropout forwards, it also flexes the axle of the rear hub, bowing it forwards. This is the sensing technique that BionX pioneered, and it offers one of the cleanest torque sensing solutions since there are no additional sensors for the user to install, as it's already built into the hub motor. A measure of axle flex like this requires careful alignment of the axle itself so that the bending moment from gravity isn't also sensed, and the scaling is similarly affected by the gear ratio of the drivechain. -
Rear Cog Torque
While the axle flex technique that BionX uses has the benefit of technical simplicity, it does not provide a truly accurate value for the human power input in watts since the amount of flex will depend on the front and rear cog selection. A more precise way to measure the pedal power from within the rear hub is with a torque sensor between the sprocket set and the hub itself. Much like the front chainring sensor, this is a rotating reference frame that complicates the transmission of the torque signal to non-rotating bike frame, but inside the hub there are techniques to do that which don't require batteries and wireless signals. The SDFSD sensor from Germany is one such sensor that is available to hub motor manufacturers. -
Pedal Force
Another place to measure pedal force is directly at the pedals itself, and since the pedal thread is one of the few things that is truly standardized across bicycles this option could offer one of the more versatile possibilities for an aftermarket / conversion kit. Pedals are on a rotating reference frame which requires a wireless coupling of the torque signal, but unlike a crank/chainring sensor they have a rotating spindle that could lend itself a small internal generator for power without the need for separate batteries. We have seen one sensor like this on the market so far from the chinese company Forehorse, which then uses ANT+ wireless communication to the rest of the system. -
Accelerometer
There's also a totally different approach to torque sensing that doesn't involve any direct force sensors at all, and that is the use of an accelerometer or other inertial sensor unit to effectively derive the force on the bicycle based on the vehicle dynamics. A simple implementation with an inclinometer type works quite well. It gives a boost when you are pedaling hard to speed up, and similarly as you go up hill and have an acceleration force due to gravity. We sponsored a university project in 2006 to build a prototype like this which worked quite well, and have been meaning ever since to develop a product around this concept. -
Spindle Deflection
Rather than accurately measuring the torque across a spindle, or the backwards pull from chain tension, the Sempu torque sensors produce a signal whenever there is stress on the cranks. Whether you have a bending force, backwards torque, forwards torque, or other stress it produces a signal. In theory this sounds like a bad idea as many of those forces don't produce any forwards propulsion power on the bike, but in practice it works surprisingly well at responding to increased pedal effort from both left and right cranks.
Effect of Flex
Regardless of the force sensing strategy, it's important that the sensor itself adds only a minimal amount of flex to the overall drivechain. We've been witness to some torque sensor implementations that had a spring with noticeable flex as torque is applied, and this resulted in a very "squishy" feeling drive chain, without a direct pedal connection to the wheel. The overall sensation as a cyclist is not good at all. Ideally, when the rear wheel is locked, the application of full torque on the pedals shouldn't move the end of the crank by more than 5-10mm.
PAS Control Schemes
We've discussed in some detail the mechanics and signals levels of pedal assist sensors, but not the actual controlling algorithm for determining how much motor power the system should apply when the rider is pedaling. There are numerous possible approaches to determining how the assist is applied. Here is a summary of the more common ones.
Basic PAS, constant power
This was the pedal assist approach used in the original "autoPAS" mode of the V3 CA device. Whenever the rider pedaled, a given amount of power was supplied to the motor. This power remained constant up to the speed limit of the system. With autoPAS set to 200watts, you would have receive the same 200 watts of boost even as you sped up or slowed down due to changing terrain or pedal power. When you adjusted the pedal assist level from the handlebar control, you would be directly increasing or decreasing this power setpoint.
Basic PAS, constant throttle
This is a common approach by many turn-key ebikes since it doesn't require any internal control loop. The PAS assist setting is basically like the throttle setpoint, so when you pedal the bike at the 50% assist level it would be like riding with 50% throttle. This generally has the effect of changing the speed limit of the bike, with 50% assist the motor will only spin up to half the speed. At lower speeds than this the motor will be able to output full power, while at higher speed there wouldn't be any assist at all. This mode can be preferable to constant power PAS for people who want their assist level to effectively regulate the cruising speed of the bike, rather than the power drawn from the battery. It is available as an option in the V3.1 CA firmware.
Cadence PAS
In a cadence controlled PAS mode, the power delivered to the motor also varies with the speed of the pedal cranks. In a normal bike with multiple gears, it is common to downshift and spin the cranks faster whenever the rider wants to put more human power into the bike, and the PAS system will respond in kind and apply more motor power as well. Setup properly, it is possible to have the ebike feel like it is responding to your pedaling effort just like it would with a torque sensor, based only on the pedal cadence.
In the case of a bike with a single speed gear, you might want the very opposite behavior, where the power is highest at low pedal RPMs when you are just starting off from a standstill or slowing down as a result of encountering a hill, and then decrease when you are pedaling fast and up to speed.
Torque Multiplier
The common approach to using a torque sensor. Either the torque or power to the motor increases in proportion to the human torque on the pedals. If you pedal twice as hard you get twice as much power. The handlebar adjustment then determines what this multiplier ratio is like, allowing you to choose between say 0.5X boost, 1X boost, or 2X boost. On the CA3, this feature is implemented by measuring the human input power in watts, and scaling that into a target output power in watts. Other systems may use the human power or torque signal to adjust the motor power via the throttle level.
Torque Multiplier with Offset
One slightly annoying detail with the simple torque multiplier scheme is that even when you are pedaling lightly the motor similarly powers up a little even though you don't need it. From the start of the CA3 releases we were also adding a baseline offset power that the rider needed to apply before any power multiplier kicked in. This way you could have a setup that rode like a normal unassisted bike with modest pedal efforts, and only when you started pedaling hard and needing the electric assist would the motor kick in. With a low threshold of like 50 watts, the power would be present even with light pedaling, while a 200 watt threshold would provide no assist during normal riding and only drive the motor when giving it plowing up hills and accelerating.
Heart rate monitor
We get asked with surprising frequency if anyone has thought of developing a PAS control that looks at a the rider's heart rate, and steps up the assistance once a certain beats per minute has been achieved to help keep the heart rate withing a target range. We're not aware of any commercial products on the market which do this, but for sure developers have been or are experimenting with it.
FAQ
Yes, of course. For some reason many people are under the impression that pedal assist and throttles are mutually exclusive. It's true that certain lines of pedal assist bike (like Bosch drives) don't provide a throttle option, but there's no logical reason for this. We're strongly in favor of always having a throttle handy to apply bursts of power when needed (such as accelerating out of a busy intersection) and to have on hand as a backup any pedal assist setup controlled with a V3 Cycle Analyst allows you to use both control inputs.
Yes! No! Maybe! This is a question that we get asked frequently, and often it's not even a question but a given assumption, i.e. I want to get a PAS sensor on my ebike for increased range. The range you get on an ebike fundamentally has nothing to do with what kind of control system you use, and everything to do with the average amount of power you draw. If with a throttle control you can't help but always ride full throttle, and a PAS sensor encourages you to ride more often at partial power levels, then yes it could increase your range. On the other hand, if you have a throttle controlled ebike and only use the throttle for steep hills etc., then the addition of a PAS setup that powers the motor all the time you are pedaling would increase your power usage and decrease your range.
On a related note, the range is also affected by how much pedal effort you as a rider are contributing. If a torque based control scheme helps encourage you to pedal harder in order to get more power from the motor, then that as well could help increase the share of propulsion power coming from your legs and result in better mileage from the battery. But it won't make any such difference if you are perfectly capable of pedaling hard without needing a torque based PAS scheme for incentive.